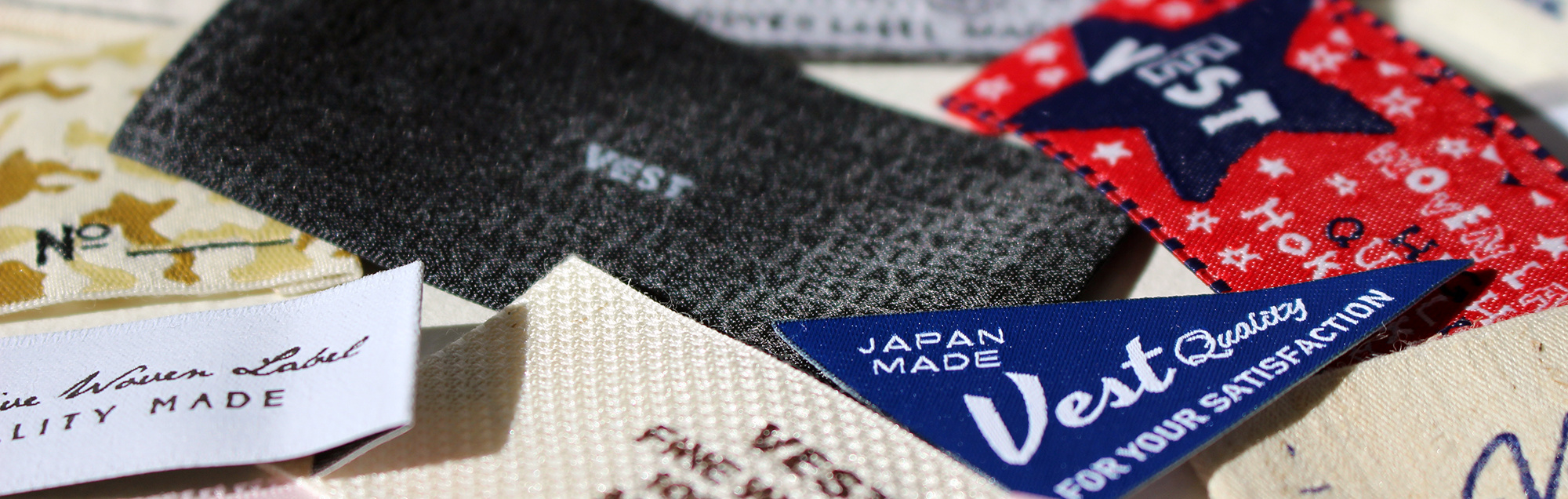
WOVEN CLOTHING LABELS PRESENTED BY VEST
The key commodities of VEST are shuttle-woven clothing labels made in Japan. They feature the aesthetic texture particular to shuttle-woven textiles, which most likely results from the minuscule air layers between the woven threads. VEST recommends shuttle-woven labels for customers who desire brand labels with an exclusive quality in these modern days while seeking higher efficiency.
In shuttle weaving, brand names and graphics are woven at the same time as the background with different threads, using the Jacquard function. The base fabric can be created as requested according to the desired textiles. Among the fundamental types of textile weaves, plain weave and satin weave are available for the base fabric, using the standard black or white thread for the warp. The looms are configured to different specifications for plain-weave and satin-weave labels. Black and white thread is always available for the warp. The thread size of the warp is 40 denier for plain weave and 60 denier for satin weave, with a different number of threads per centimeter depending on the weave.On the other hand, the fabric width is common to both weaves: eight sizes of 9, 12, 15, 18, 24, 30, 36 and 51 mm. In summary, at least thirty-two looms are necessary for plain weave and satin weave, using black and white warp thread, respectively. However, according to popular colors and widths, we can flexibly respond to the requirements of each customer in cooperation with our subcontractor factories.
In addition to these fundamental weaves, we also provide customers with various labels of special weaves (e.g., grosgrain, basket weave, rolled selvage and double cloth) in combination with different types of yarn (e.g., cotton, wool, and hemp blends) that meet their needs.
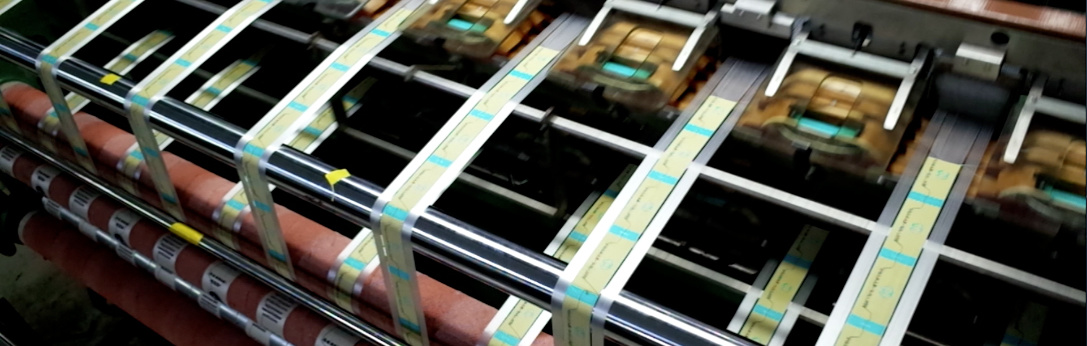
FUNDAMENTAL WEAVES FOR BASE FABRIC
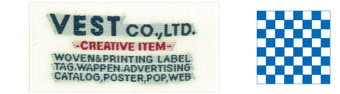
PLAIN WEAVE
In plain weave, warp and weft threads crisscross each other in a one-over, one-under sequence, and the front and back textures are the same. The main feature of this weave is that it reproduces a detailed design. The label surface, having an even ratio of warp and weft threads, creates a Chambray-like or iridescent texture if their colors are different. White warp thread makes the textile lighter than the selected weft color while black warp thread makes it darker than the weft color.
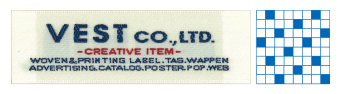
SATIN WEAVE
Satin-weave fabric is available in two types: regular satin that is lustrous with more warp threads than weft threads appearing on the surface; and reverse satin of a color that looks almost the same as that of the weft threads with more weft threads appearing on the surface. Compared with plain weave, the fabric is voluminous with a luxurious appearance. However, satin-weave fabric is not suited to finely detailed designs. Higher density weaving can improve matters, but the labels then become stiff and thick.
CHARACTERISTICS OF WOVEN CLOTHING LABELS BY MATERIAL
①SILK LABELS ▶ For elegant clothing and formal attire
With fine threads, it is possible to produce a sophisticated sheen and texture as well as delicate weave patterns. However, silk dissolves in chlorine bleach and is not suitable for dyeing or washing of products. Silk labels are less cost-competitive than polyester labels with the same specifications. #Labels with warp, weft and pattern threads all of silk (the base fabric is satin weave #Labels with weft and pattern threads of silk, and warp thread of cuprammonium rayon (the base fabric is satin weave only)
②RAYON LABELS ▶ For classic casual and work wear, and traditional military products
The thick pattern threads of rayon produce a more vintage feel, reproducing the patterns with various combinations of dots. Rayon dissolves in chlorine bleach in the same way as silk. However, it can be dyed with colors for cotton. Rayon labels are dyed together with products of the same color. Regarding durability, rayon labels are weaker than polyester labels and will shrink when washed. The cost is similar to polyester labels with the same specifications. #Labels with weft and pattern threads of rayon, and warp thread of polyester (the base fabric is either plain or satin weave)
③POLYESTER LABELS ▶ For standard products
Currently, polyester labels are the mainstream in the woven clothing label industry. Among the reasons for its popularity are ease of weaving, processing and handling; stable color yarn supply and cost-competitiveness; and stability of physical properties. #Labels with warp, weft and pattern threads all of polyester (the base fabric is either plain or satin weave)
④COTTON LABELS ▶ For natural casual products
Reverse satin weave with the base cotton thread appearing on the surface can add a more cotton-like texture to the fabric. Using different types of yarn for the base and pattern threads extends its usage as a dyeable label. Even if the base fabric is dyed, the brand logo or other pattern still stands out. In addition, using cotton for the base creates a surface that is gentle to the skin and can reduce any prickling sensation. #Labels with weft thread of cotton, and warp and pattern threads of polyester (the base fabric is standard satin weave)
⑤LABELS USING DIFFERENT TYPES OF YARN
In the same way as cotton labels, a yarn blend of wool, hemp, etc. is used for the weft thread with polyester for the warp thread. Thread with a single yarn size of around 30 cotton count can be woven into clothing labels. It is possible to create seasonal or conceptual labels using this thread (the base fabric is standard satin weave).
HISTORY OF WOVEN CLOTHING LABELS IN THE HOKURIKU REGION OF JAPAN
Around 1910, woven clothing labels from Britain were introduced in Japan to give clothes an element of prestige. Domestic production of woven labels began in 1911, using a special handloom invented by Mr. Teraoka from Amagasaki, Hyogo. The loom combined the features of a Jacquard mechanical loom used for traditional fabric production in Kyoto, Nishijin, with a machine that could produce multiple fabrics simultaneously. Later, in the 1920s, handlooms were upgraded to powered ones. Hokuriku, in the northwestern part of Japan, was already involved in ribbon production and thus developed as a woven label manufacturing region before others.
In the 1930s, the use of woven labels was mostly limited to military clothing. In the 1940s, the woven label industry in Hokuriku enjoyed a prosperous period due to huge orders from the United States that exceeded the capability of the region’s manufacturers. However, during the following decade, the industry experienced considerable turbulence, with repeated episodes of boom and bust. Within just ten years, the number of factories producing labels increased five-fold, causing excessive competition among the manufacturers, many of whom were driven out of business. In addition, the market price of rayon (artificial silk) for the labels plunged and remained at a low level. Finally, the entire industry went into recession.
In the 1960s, the Tokyo Olympics helped the economy bounce back, which triggered the rapid Westernization of the lifestyle and clothing of the Japanese. Along with the spread of casual fashion, the demand for woven clothing labels increased. In the meantime, the introduction of acid synthetic detergents and bleaches caused problems with color fading and shrinkage of rayon labels that were dominantly used at the time. As a solution, cuprammonium rayon and polyester yarn were introduced. This not only improved the ease of weaving and cost competitiveness but also reduced the labor for starching, etc. In recent years, polyester labels have become the mainstream in the industry.
Silk labels: Elegant items
Rayon (artificial silk) labels: Mainstream up to the 1960s
Cuprammonium rayon labels: Alternative to rayon labels (currently, seldom used) Polyester labels: Alternative to rayon labels (current mainstream)
Innovation also occurred in the development of looms. Traditional shuttle looms were replaced with rapier looms designed for wide fabrics, which enabled high-speed mass production. Conventionally, background designs required mongami pattern cards, which consisted of dozens of thick punch cards strung together, requiring extensive time and skill for the weaving operation. However, with the advance of computerization, paper patterns were converted into digital data, which shortened the time required for production.